U.S. Auto Workers Face Competition from Other Nations and New Technology
President Trump vows to return auto jobs to the U.S. But experts say automation is the likely future of auto industry.
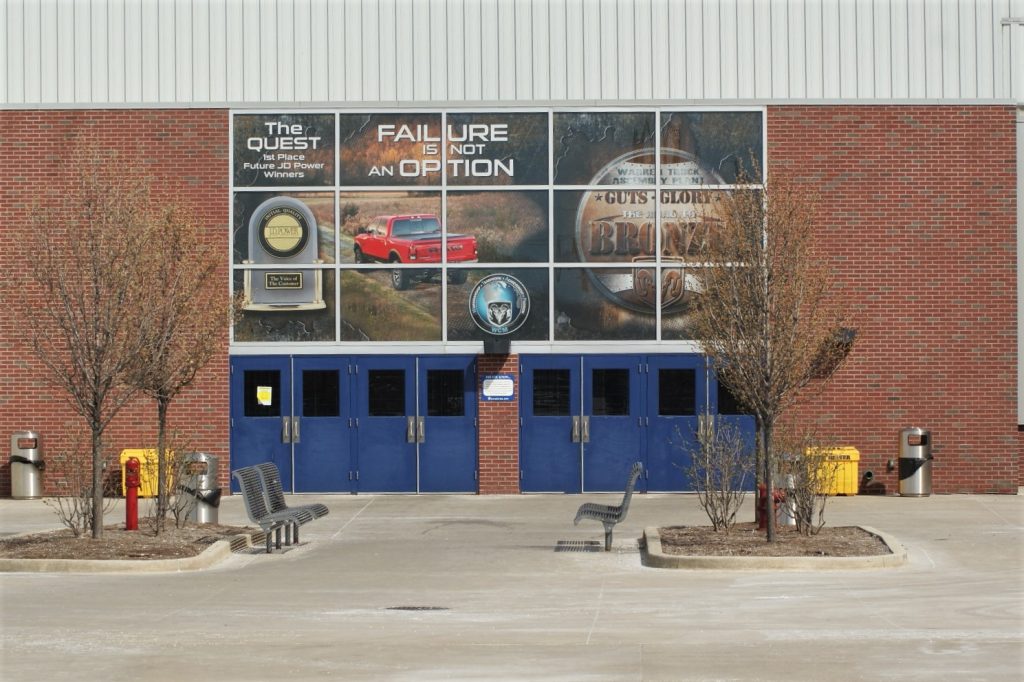

President Trump has repeatedly pledged to bring outsourced auto jobs back to the U.S. and make Michigan the manufacturing hub of the world.
But will today’s auto workers be ready for the rubber to meet the road in an increasingly technological future?
As part of The Takeaway‘s Rockefeller Urban Resilience Project, WDET examined the role of auto workers, a group whose resiliency is being tested by reality.
A Presidential Vow
In the heat of the presidential campaign last year, then-candidate Donald Trump made a vow that still echoes among car companies and the auto workers who eventually helped propel him into the Oval Office.
Trump said if he were elected president and the Ford Motor Company made good on plans to open a new factory in Mexico, he would impose as much as a 35% tax on any products made south of the border but sold in the U.S.
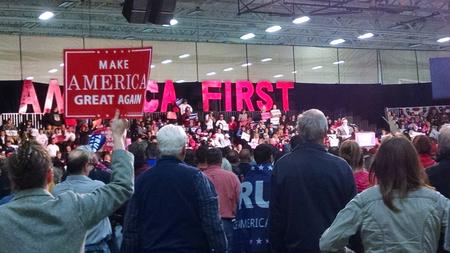
“Within 24 to 48 hours I will get a call from the head of Ford,” Trump predicted. “And he will say, ‘Mr. President, we have decided that we will build our new plant in the United States.’ ”
And that message resonated among blue-collar workers in Macomb County, where voters helped deliver the state, and the presidency, to Trump.
Fiat Chrysler Automobiles worker Elsie Martinez, for one, gives Trump and his push to bring auto jobs back to the U.S. a big-league thumbs-up.
Martinez says, “I love it, I love it. Americans, we shop here, we do our jobs here, we need to keep our money here. We can’t compete with people who can work for a dollar a day.”
Mexico or Machines?
Experts say the U.S. has lost more than 5 million manufacturing jobs since the year 2000, while jobs in service industries increased.
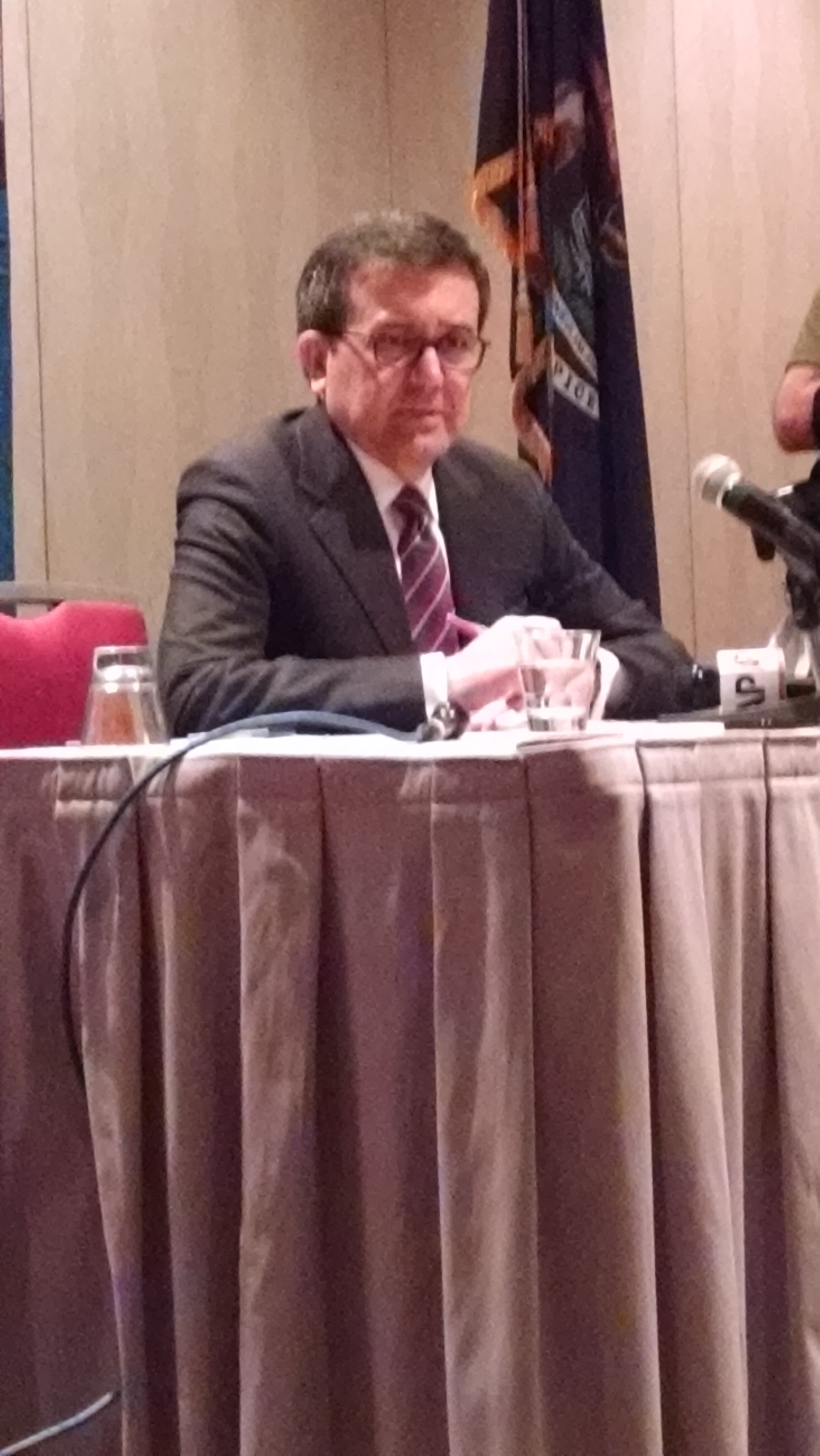
But Mexico’s Economy Minister Ildefonso Guajardo says don’t blame his country.
He recently told Detroit business executives he was ready to negotiate revising the North American Free Trade Agreement with President Trump.
“Fighting for 700 jobs will not make a difference. It is how we are going to readapt (and) redesign our training process.” – Mexico’s Economy Minister Ildefonso Guajardo
But Guajardo says there needs to be an understanding that it’s automation, not Mexico, with which U.S. auto workers truly must cope.
“Fighting for 700 jobs will not make a difference,” he says. “It is how we are going to re-adapt (and) redesign our training process to face together the challenges of the technological revolution.”
To the head of the United Auto Workers union, that spells one word:
Robots.
UAW President Dennis Williams says U.S. auto workers are in something of a battle against the R2-D2’s of the car world
He says the U.S. needs to arm workers with a national industrial policy that helps employees learn new skills.
”Education has to get back to not only the academic part of education but also the vocational and the apprenticeship part,” Williams says. “You gotta have a skill level in the country to maintain industrial bases and technology.”
Building the Auto Worker of Tomorrow
The auto industry of the future is on display at an educational event hosted by Junior Achievement of Southeastern Michigan.
Hundreds of high schoolers filter between exhibits featuring car companies and recruiters, touting jobs they say pay auto workers well, if not exactly CEO-level salaries.
“You will not have the huge workforce that we’ve had in the past. Technology has moved on.” – Elizabeth Griffith, Faurecia Interior Systems
A recruiter from General Motors even strikes a note of levity, telling the assembled students an auto worker at his company typically won’t be driving a Ferrari, “Because they work at GM. Why would they drive a Ferrari? Ha!”
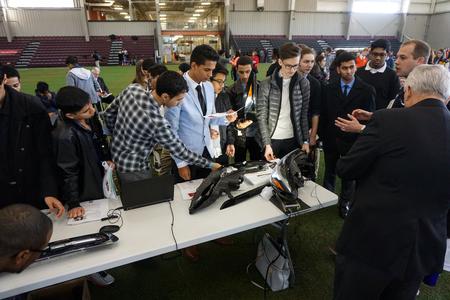
But building the high-tech car parts the students are examining demands that workers know something about advanced technology.
The Director of Engineering for global car interior design company Faurecia Interior Systems, Elizabeth Griffith, says the days of assembly line workers making part after part are rapidly dwindling.
Robots, she says, work faster and more efficiently without requiring vacations or sick days.
“So you will not have the huge workforce that we’ve had in the past. Technology has moved on. With autonomous vehicles and everything else going on, you will not have that luxury in the future. Okay? Because you just can’t,” Griffith says.
She notes that her company actually fostered some apprenticeship programs to try to create the kind of skilled workforce it needs.
But Griffith says convincing auto workers to adapt to the new normal of manufacturing can be a tough sell.
Even, she says, in her own household.
“I come from a blue-collar family. I grew up in Detroit. My Dad worked in the automotive industry, my brother works in the automotive industry currently. I’m married to a UAW member. So it’s very controversial sometimes in our family,” Griffith says.
“But you have to (ask) are they willing to be retrained? And in a lot of cases they will flat out tell you ‘No I can’t do that.’ “
Cobots and a Conundrum
Yet it’s a reality workers contend with daily back in Macomb County, at factories like the Fiat Chrysler assembly plant in the city of Warren.
It is shift change at the plant and workers are leaving for the day.
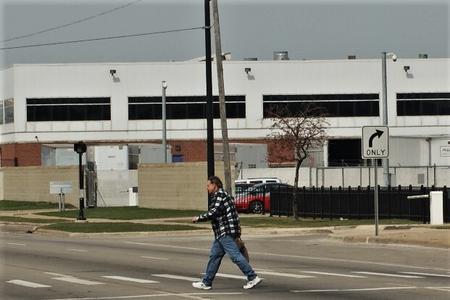
Veteran employees like 18-year maintenance worker Mike Nicholson say they are sure their jobs will be there when they return the next day, robots or not.
Nicholson says, “People on the line get replaced with robots. But they can’t really replace maintenance guys with robots. So yeah, it’s unfortunate if you’re on the line.”
For worker Christopher Cavaretta, increased automation actually provides an opportunity. There’s even a term for it. They’re known as “cobots,” humans working side by metallic side with robots.
“You just gotta get the right knowledge to learn how to work the robots, then you’ll be fine. Right? But that could be a problem for the ‘working class.’ I’m fine ‘cause I got multiple streams of income. I do real estate too,” Cavaretta says.
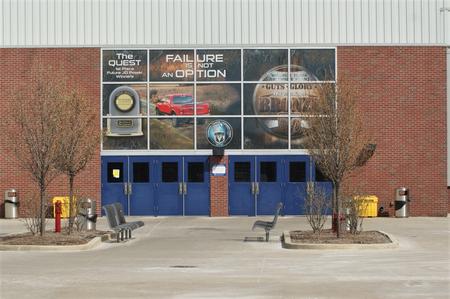
Other auto workers, like 23-year-old Frederick Miller, say the assembly plant offers a decent, if physical, job. For now.
Miller says, “I think it’s not for everybody. We had a guy go to the emergency (room) because of some of the jobs in here. It’s not for me, not for the rest of my life. Think I can do something better than this. I’m still young.”
The U.S. auto industry has proven extremely resilient, posting record profits only a few years after two of Detroit’s Big 3 automakers required a federal financial bailout to stay afloat.
But the question remains whether the auto workers of today will seek the new skills necessary to remain relevant in an increasingly automated future.
Or will they will look elsewhere, as some workers indicate they already are, as the auto jobs of the past continue to fade away?