CuriosiD: Former Tenant of this Man’s Apartment Reformed the Auto Industry
Shelby Jouppi July 10, 2015Listener Josh Wilt’s asks, “What was the history of Norton Company located in Woodbridge?”
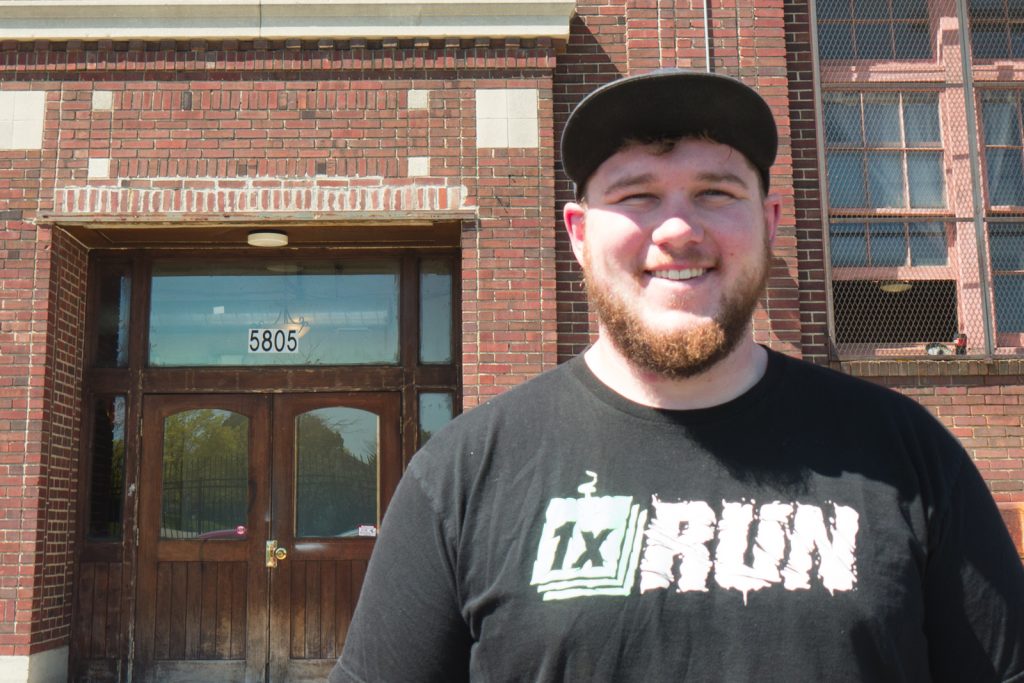
Photo credit: Shelby Jouppi
For this edition of CuriosiD, we tackle a question from listener Josh Wilt.
“What was the history of the Norton company located at 5805 Lincoln Street in Woodbridge?”- Josh Wilt
Sticking out of Josh Wilt’s bedroom floor are large brass machine fittings. His apartment sits on the third floor of the Universal Lofts, an imposing industrial-looking building in Detroit’s Woodbridge neighborhood.
Josh wondered what machinery might have occupied his bedroom at one point in time. He also noted a large “Norton” logo on the front facade of the building and in tilework in the entrance, that made him reach out to CuriosiD asking, “What was the Norton company, and what did it produce?”
The short answer
Josh’s building was, in fact, built for the Norton Company in 1927. Norton’s headquarters were in Worcester, Mass., but the company used this facility as a district office and warehouse for final-stage manufacturing.
Norton’s products were abrasives and grinding wheels, which we will get into later. And it turns out that these products played a crucial role in mass machine production.
In fact, in 1920 Henry Ford credited the abrasive process with allowing his company to make the Model-T affordable.
“In 1920, Henry Ford credited the abrasive process (what Norton products were used for) with allowing his company to make the Model-T affordable.”
Machines inspired by fine ceramic pottery
Before Norton Company was known by that name, it began as a small pottery shop on the streets of Worcester, Mass.
Cousins Franklin Norton and Frederick Hancock opened F.B. Norton Pottery in 1858.
A few decades later, employees at the shop discovered that the pottery-making process of kiln firing could be applied to the manufacturing of grinding wheels. These wheels are used to shape metal to extremely precise measurements.
Grinding wheels existed prior to Norton, but were made of wood and had grains of emery (an abrasive) glued to the outside. This made for shoddy and imprecise grinding. Norton employees mixed clay, emery and water and fired the wheel in a kiln.
Norton expanded the business to include manufacturing these wheels, and demand for their product skyrocketed.
In 1885, Franklin Norton sold the business to go back to pottery-making. But the company held on to the Norton name.
Making automobiles affordable
Lindsay Brooke is the Senior Editor of Automotive Engineering Magazine. He also wrote a book on the Model-T.
Brooke explains that when making metal parts that have to fit or work together very closely, that part just about always needs to be shaped and fine-tuned to the thousandth of an inch.
“Engines and axles and automotive drive trains have a lot of these parts,” he says.
Norton’s grinding machines made this process faster, more precise and extremely efficient.
So, in 1914, when Henry Ford was looking to reduce the cost of manufacturing his vehicles, he invested $30,000 in automated grinding equipment from Norton. By doing this, Ford could replace human labor on other machines.
“In 1920, when the Rouge plant was finally up and running and Ford has this colossal empire,” says Brooke, “he made the comment that if he hadn’t invested in automated grinding equipment, …
“the Model-T would have been thousands of dollars instead of less than three hundred dollars.”
Bernie Meyer, Norton’s former executive vice president of operations, says Norton played a huge role in the auto industry as a whole.
“You could make cars, instead of making one a day, you could make one in minutes or less than a minute,” he says. “It wasn’t just grinding wheels or abrasives that did it; there were lots of things, but that was a very important component in it.”
What about Josh’s building?
Meyer started with the Norton Company in 1958. He lives in Massachusetts, but remembered the building in Detroit – Josh’s now apartment building.
“They were warehouses primarily – places where we could stock products for the industry,” he says. “In some cases there was a minor amount of work done on those products before they were shipped to customers there.”
What about the machines that would have been bolted to the floor in Josh’s bedroom?
He says those were most likely “truing machines” — high-speed turning devices, like a lathe, which modified grinding wheels to the customers’ needs.
Norton Company today
Josh had one other question that we didn’t get around to – When did the Norton Company close? It didn’t.
In 1990, the Paris-based Saint-Gobain Corporation acquired Norton. Now called Saint-Gobain Abrasives, the company’s headquarters are still in Worcester, Mass. In fact, the Norton brand is celebrating its 130th anniversary this year.
“Saint-Gobain Abrasives is the leading supplier of abrasives globally,” says Brad Johnson, the company’s vice president. “We have 64 plants in 28 countries around the world manufacturing all aspects of abrasives.”
The company that started in a small pottery shop now employees 3,000 people in North America and 11,000 globally.
Special thanks to folks at Saint-Gobain Abrasives, Inc. for connecting us with Bernie Meyer and providing the incredible images above in partnership with the Worcester Historical Museum.